GKG G-TERA Solder paste printer
The new generation of automatic printing presses, the all-new G-Tera, is equipped with a 3.0-megapixel LIGHT-Bolt CCD camera, an upgraded conveyor system, and an enhanced printing system. It reduces the actual cycle time by up to 40% compared to other GKG SMT printers. The G-Tera utilizes a high-precision servo-driven dynamic system to ensure fast and accurate alignment. With its independent cleaning system, it capable to print ultra-fine pitch pads as small as 0201 metric, guaranteeing high-quality solder paste printing and boosting production efficiency.
The entire machine is computer-controlled, featuring a user-friendly operating interface and a wide range of software functions. It is built with “ready for the future” functionality, making it the smartest and most future-proof machine in the GKG SMT printer series.
LIGHTNING SPEED
Core Cycle Time : 5.2 secs | Actual Cycle Time : 12.5 secs
The upgraded linear motor-driven ‘LIGHT-Bolt’ fiducial camera (3.0 megapixel, FOV: 8 x 10 mm) moves and captures stencil and PCB fiducial marks concurrently at lightning speed.
The single-stage or 3-stage mode is automatically generated through programming. When converting to 3-stage mode, the conveyor system is able to pre-loaded PCB to reduce loading and unloading time.

The upgraded linear motor-driven cleaning system is able to operate independently without relying on external power, significantly reducing cleaning stroke delay time.

UNMATCHED ACCURACY
Wet Print Capability : ± 12.5 um @ 6 sigma, ≥2 Cmk
The squeegee pressure feedback and dual cylinder driven squeegee structure design provide real-time pressure monitoring, preventing uneven printing distribution on large boards and ensuring a printing pressure accuracy of ±0.2 kg.

Stencil Lock utilizing a vacuum hold-down mechanism to secure the stencil firmly on both sides of the conveyor rail, ensuring firm contact with the PCB during printing and eliminating the stencil ‘waving’ effect.

The real time Print Table Height (Z axis) Monitoring System, which monitoring the print table up/down accuracy within 15 microns.
VERSATILE CAPABILITY
Real-time monitoring of paste rolling diameter within a controlled range. Ensuring an optimal paste quantity on the stencil surface, while maintaining the rolling speed during printing cycle for optimal quality control.

Providing consistent edge-to-edge printing, the conveyor system is equipped with hidden fixed top foil clamps on both sides of the conveyor edge that can be slid out manually and used concurrently with the motorized auto edge clamp for thin PCB printing.
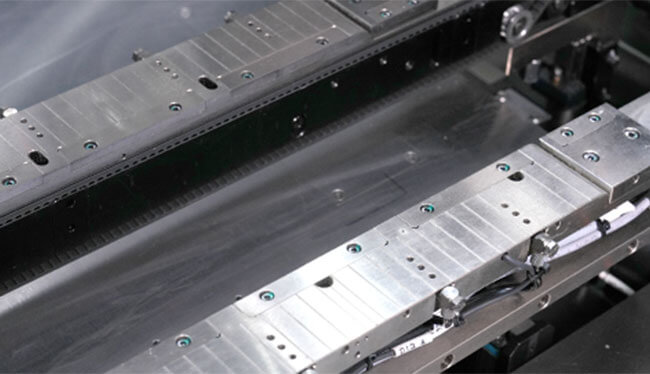
Go Green, Go Paperless!! The newly invented paperless and self-cleaning stencil cleaning system combining vacuum suction and scraper, significantly improving cleaning results and drastically reducing the usage of IPA and lint-free paper.

FUTURE PROOF SOLUTION
Compatible with either glue dispensing or solder paste dispensing. Featuring with two types of jetting valves, allowing for dispensing after printing.
AGV assisted automatic stencil changing is triggered by commands from MES server. The AGV delivers the new stencil and collects the used stencil from the rear side of the printer, pairing with the automatic solder paste collection function to achieve zero human intervention.

The automatic solder paste collection function is equipped with an auto paper roller to collects retained solder paste on the stencil surface and transfers it to a new stencil surface after stencil changing. This feature pairs with the AGV assisted auto stencil changing function to achieve zero human intervention.

The facial recognition authorization system utilizes facial recognition technology to provide machine access control and ergonomically adjust the display height according to user’s specific preferences for optimal comfort.

Stencil aperture inspection system is programmable to perform automatic inspections after a set number of printing cycles. Automatically triggering cleaning stroke if clogged apertures are detected.
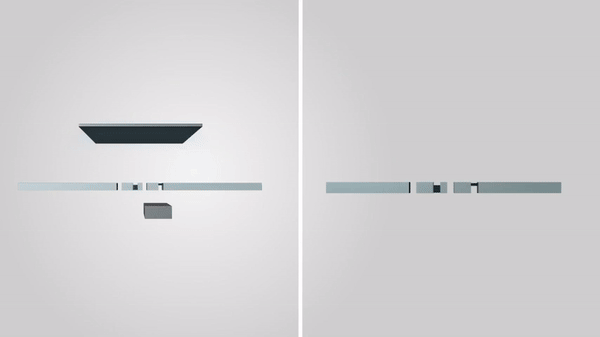
The Auto Paste Replenishment System able to hold two 500g cans of solder paste to replenish it automatically.
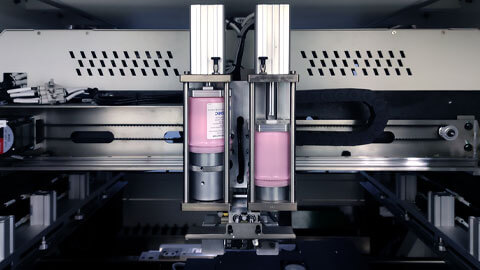
SPECIFICATION
Performance |
|
Machine Alignment Capability |
±8µm @ 6σ (CPK≥2.0) |
Process Alignment Capability |
±12.5µm @ 6σ (CMK≥2.0) |
Core Cycle Time |
5.2 secs |
(excluding printing & cleaning time) |
|
Actual Cycle Time |
12.5 secs |
(including printing & cleaning time) |
|
Product Changeover Time |
2 mins |
New Product Set-up Time |
4 mins |
PRINTING PARAMETERS |
|
Print Speed |
10~200 mm/s |
Print Pressure |
0.5 – 20kg |
Print Mode |
Single or Dual squeegee printing |
Squeegee Type |
Std: OPC Squegee |
Opt: Metal / Rubber / 2 Steps Squeegee |
|
Snap Off Distance |
0-20mm |
Snap Off Speed |
0-20mm/s |
Stencil Frame Size (L x W) |
Adjustable, 470 mm x 370 mm to 737 mm x 737 mm |
Stencil Positioning Method |
Automatic Y-direction positioning |
Cleaning System |
2 in 1 Paperless self cleaning dry & secondary wet lint-free paper with vacuum suction (software select) |
Board Handling |
|
Max. Size (L x W) |
Single Stage : 510 mm x 510 mm |
3-Stage : 265mm x 510mm (Optional 400mm x 510mm) |
|
Min. Size (L x W) |
50 mm x 50 mm |
Board Thickness |
0.4~6 mm |
PCB Thickness Adjustment |
Automatic Height Adjust Platform |
PCB Max. Weight |
5 kg |
PCB Edge Clearance |
2.5 mm |
PCB Bottom Clearance |
20 mm |
Conveyor Height |
900 ± 30mm |
MAX. Conveyor Speed |
1500mm / s |
Conveyor Belt |
U-Shape Belt |
Conveyor Direction |
L to R, R to L, R to R, L to L |
Support Method |
Magnetic support pins, bars, dedicated vacuum block |
Clamping Method |
Auto Motorized Edge Clamp / Manual Hidden Fixed Top Foil Clamp |
OPTICAL SYSTEM |
|
Field-of-View (FOV) |
10mm x 8mm |
CCD Camera |
3.0 MP CCD Digital camera look up & down concurrently |
Fiducial Types |
Circle, triangle, square, diamond, cross |
Fiducial Size |
0.1~6.0 mm |
Number of Fiducial |
2 – 4pcs |
Facility Requirement |
|
Power Supply |
AC220±10%, 50/60Hz 2.2kW |
Air Supply |
4~6kgf/cm² |
Air Consumption |
~5L/min |
Working Temperature |
-20°C ~ +45°C |
Dimension (Excluding signal light) |
1,258(L) x 1,540(W) x 1,520(H) mm |
Machine Weight |
1,250kg ~ 1,300kg |
Efficient Technology Co.,Ltd provide a full SMT assembly line solutions, including SMT Production Line, SMT Pick and place machine, SMT Stencil Printer, SMT Inspection equipment, SMT Weling equipment, SMT Intelligent Storage System, SMT Automatic Insertion Machine, SMT Peripheral Equipment, SMT Feeders, SMT Nozzles, SMT Spare Parts etc any kind SMT machines you may need, please contact us for more information: WeChat: +8613714564591 Email: sales@efsmt.com
FAQ:
Q: What we can do for you?
A: One-stop SMT Solution Supplier; Reliable SMT Partner.
Q.What is your MOQ requirement for the machine?
A. 1 set moq requirement for the machine.
Q. This is the first i use this kind of machine, is it easy to operate?
A: Provide free training,There are also English manuals or instructional videos to show you how to use the machine.
Q: If the machine has any problem after we receive it, how can we do?
A: Our engineer will help to solve it first, and free parts send to you in machine warranty period.
Q: Do you provide any warranty for the machine?
A: Yes 1 year warranty will be provided for the machine.
Q: What is your payment terms?
A: 30% deposit in advance and 70% balance before shipment.